Are you unsure about the main points of comparison when looking at sterile tube welding vs. aseptic connectors?
Use the table below to learn more about which solution is best for your unique application needs.
How do aseptic quick connectors compare vs. sterile tube welding?
Factor |
Sterile Tube Welding |
Aseptic Quick Connectors |
Set-up/Use Time |
Slower vs. aseptic because you have to move sterile tube fuser into position, obtain and install the correctly sized tubing holder, initialize the welder, load tubing, weld, cure time (~4-7 minutes total)
Set up/use time multiplied by hundreds of welds a week affects overall productivity (e.g., 100 welds/week x 4 minutes = 6.67 hours operator time for welding)
|
Aseptic connectors are sterilized and ready to go in tubing/bag assembly, requiring only seconds to connect and actuate
|
System Flexibility |
Connection can be made at any time or any place in the tubing
Welder must be set up for correct tubing size and material
Tube holders are gauged to specific sizes (e.g., 3/8” x 5/8”)
Only the same-size tubing (same ID and OD) can be welded together
|
Single-use connectors are available that allow for flexibility between different types and sizes of tubing
No reducers required
|
Acquisition/Use Costs |
Capital equipment and ancillary equipment costs range from a few thousand dollars to tens of thousands per welder in each clean room
Single-use blades cost
Staff time for set-up and use or downtime if system jams or locks
Back-up welder if needed
Maintenance cost
|
Higher variable costs than blades
No capital expense
|
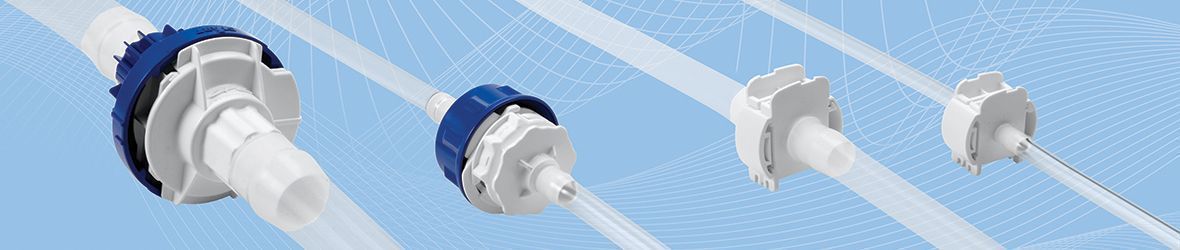
Factor |
Sterile Tube Welding |
Aseptic Quick Connectors |
Maintenance Requirements |
Welders must be in good working order
Welder manufacturer’s warranties for regular preventative maintenance of equipment
Need backup welder during maintenance or out-of-service episodes
|
Single-use disposable connectors ready to use
No maintenance required
|
Extractables Package |
Very limited package
Published studies on the impact of thermal welding process to the flow path of the tubing
|
Most manufacturers provide a published extractables package to understand potential effects on cell lines.
|
Contamination Risks |
Nonconformance to manufacturer’s recommendations might raise contamination risk due to:
- Placing tubing with the incorrect diameter in the tube holder. This can cause small pinholes in the weld, due to pinching or squeezing the tubing out of the holder during the weld process
- Welding different tubing types together, which can lead to weld failure
|
Little to no contamination risk because validated aseptic connectors maintain a sterile boundary adjoining two single-use systems.
|
Staff Training |
Welders require operator training to ensure proper technique, minimize errors and to safely use the equipment
|
Largely connect-and-go, self-contained components with minimal operator training required
|
Potential for Operator Error |
Not following manufacturer’s recommendations can lead to the following potential operator errors:
- Using wrong tube holders for size of tubing
- Using incorrect tubing: silicone, mismatched TPE
- Using incorrect tubing type setting on the welder
- Not using long enough tubing
- Putting tension on the tubing
- Inserting the blade incorrectly or reusing single-use blades
|
Not following manufacturer’s recommendations can lead to the following potential operator errors:
- Using process fluids outside of the connector’s chemical compatibility specifications
- Not fully attaching connector to tubing
- Applying too much side load
|
Materials Considerations |
Minimum tubing lengths might be required to fit tubing into welder
Must connect same materials (e.g., C-Flex to C-Flex)
Costly C-Flex tubing is often used for welding
Silicone can’t be welded because the material burns
Must know each vendor’s type/size of tubing to ensure compatibility of supplies
|
Any tubing length — no minimums required
Connect to any type of tubing, including silicone, and different types of tubing (e.g., silicone to C-Flex)
Connect different hose barb sizes (e.g., one side with ¾” hose barb and the other with a ½” hose barb)
Genderless connectors eliminate the need to carry male/female components
Connectors from the same family can be interconnected
|
Level of Validation |
New sterile tube welders require onsite validation but come with a full weld validation package
No new product contact material will be introduced into the process
|
Aseptic connectors are ready to use and have been validated for material biocompatibility, extractables, sterility, and leakage
New product contact material might need to be introduced and tested if the connector material has not been used elsewhere in the process
|
Wet Welding |
Weld on a new bag at any time or any place in the tubing line (e.g., during a perfusion process). Sufficient tubing length is required to make the weld
|
A pre-assembled, sterilized manifold of aseptic connectors facilitates adding additional lines to a process
|
Operating Conditions |
Ensure sufficient room and ample tubing to place welder near the process due to the size of the welder
|
No extra space, materials or equipment required for connector use
|
Product Weight |
~25 - 35 lbs. for welder
|
Negligible weight per connector
|
When it comes to sterile tube welding vs. aseptic connectors — which is best for my application?
When properly applied, either sterile tubing welders or aseptic connectors can create reliable connections.
The one you choose will depend on the unique features of your application. Factors such as ease of use, potential for downtime, risk for operator error, cost and supply management take on added importance when making this consideration. In most cases, however, aseptic connectors — particularly genderless models—deliver the flexibility, ease of use, reliability and cost efficiencies sought by today’s bioprocessors.
Have more questions about aseptic connectors?
You can connect with a member of our sales team by filling out our contact form.
References:
1. “Friday’s Five Questions for the Biotechnology Community” Survey. Aspen Alert. Issue 2441: 8 June 2017.